Ситаллы
представляют собой стеклокристаллические (микрокристаллические) материалы,
получаемые путем направленной (катализированной) кристаллизации стекол
специальных составов, протекающей в объеме заранее отформованного изделия.
Ситаллы состоят из одной или нескольких кристаллических
фаз, равномерно распределенных в стекловидной фазе.
Впервые поликристаллическое "фарфоровое" изделие, способное без деформаций
выдерживать высокие температуры, получил при кристаллизации стекла французский
химик Р.Реомюр в 1739 г. Вновь его идея возродилась лишь в конце 20-х
годов ХХ века, когда в ряде стран были созданы стеклокристаллические материалы
с ценными техническими свойствами. В СССР наиболее интенсивно исследования
в этой области проводились в Московском химико-технологическом институте
им. Д.И.Менделеева. Существенным успехом была разработка в конце 50-х
годов в США "пирокерамов", нашедших применение в производстве тепловых
экранов (наконечников) для управляемых реактивных снарядов.
Главная особенность ситаллов - тонкозернистая
равномерная стеклокристаллическая структура, обусловливающая
сочетание высокой твердости и механической прочности
с отличными электроизоляционными свойствами, высокой температурой размягчения,
хорошей термической и химической стойкостью. В ситаллах, изготовленных
из светочувствительных стекол, получают непрозрачные белые или цветные
трехмерные изображения. Различная растворимость
кристаллической и прозрачной стекловидной фаз открывает возможности получения
выпуклого изображения и производства из фотоситаллов технических изделий
с сеткой прецизионно выполненных отверстий любого сечения.
Термическая устойчивость ситаллов обеспечивается очень
небольшими, а иногда и отрицательными (от -7
10-7 до +3
10-7) коэффициентами
термического расширения.
Оптическое кварцевое стекло может быть заменено прозрачными ситаллами,
которые имеют перед ним то преимущество, что в силу малых коэффициентов
теплового расширения они нечувствительны к тепловым ударам. Прозрачность
связана с размером кристаллов, меньшим длины полуволны видимого света
(сотые доли м), и близостью показателей
их преломления к стекловидной фазе. Светочувствительные стекла и фотоситаллы
находят широкое применение в микроэлектронике, ракетной технике, космосе,
оптике, полиграфии и бытовых приборах. Так, из фоточувствительного стекла
получены матрицы для газоразрядных приборов, фотокерам для изготовления
плат печатного монтажа, из фотоситалла - перфорированные диски, применяемые
в катодно-лучевых трубках и т.д.
Технология ситаллов включает
стадии (1) варки стекла, (2) формовки изделий и (3) специальной термической
обработки.
Первые две стадии проводят обычными методами,
рассмотренными в предыдущем
разделе. Технические ситаллы получают на основе искусственных шихт
тех частей силикатных систем, в которых кристаллизуются фазы, обладающие
заданными свойствами. Для термостойких ситаллов такими фазами являются
кордиерит, сподумен LiAlSi2O6,
эвкриптит LiAlSiO4;
для высокопрочных - шпинель, муллит;
для диэлектриков - кордиерит, диопсид,
волластонит и т.д. Такие свойства, как плотность,
коэффициент термического расширения, теплопроводность, модуль упругости
и диэлектрическая проницаемость зависят от свойств фаз и аддитивно меняются
с изменением содержаний этих фаз. Поэтому важнейшую задачу технической
петрологии составляет изучение диаграмм состояния соответствующих систем.
На фазовый состав ситаллов влияют малые (до 1,5%) добавки модификаторов
(Na, K, Ca, Ba и др.), стеклообразователей
(В, Р и др.) и окислов промежуточного типа, введение которых не
меняет состав основных фаз, но заметно увеличивает или снижает их содержание.
Необходимыми добавками являются вещества, служащие катализаторами
и центрами кристаллизации стекол.
В качестве последних применяются: металлические
Au, Ag, Cu, Pt, Pd в
количествах от сотых до десятых долей %; окисные TiO2,
P2O5, Cr2O3, ZrO2,
ZnO и др. (первые %), фторидные Na3AlF6,
Na2SiF6, CaF2
и др. (обязательно совместно с Al2O3),
сера или сульфаты с добавкой кокса, сульфиды. В
состав фотоситаллов вводят в качестве светочувствительных добавок
Au, Ag, Cu в сочетании с сенсибилизаторами. Сенсибилизаторы
- вещества, способствующие более полному протеканию фотохимических процессов
- повышению фоточувствительности с образованием скрытого поверхностного
изображения. При получении фотохромных и других светочувствительных стекол
в качестве сенсибилизаторов используются GeO2,
одновалентное золото, сернистые соединения щелочных металлов и др. Применение
элементов платиновой группы (Pt, Re, Pd, Os, Ir)
не требует присутствия сенсибилизаторов.
С целью удешевления производства и комплексного использования сырья для
изготовления ситаллов привлечены: доменный шлак вместе с кварцевым песком
- для получения шлакоситаллов; магматические эффузивные и интрузивные
горные породы основного состава (базальты, габбро, траппы), метаморфические
породы (тремолитовые и тальковые сланцы), осадочные породы (лессовые суглинки,
известковая глина), нефелиновый концентрат - для получения петроситаллов.
Оценка пригодности шлаков и горных пород для этих целей наиболее просто
и эффективно осуществляется петрографическими методами по их минеральному
составу. Не последнюю роль играют знания петрохимических особенностей
и использование возможностей методов петрохимических пересчетов.
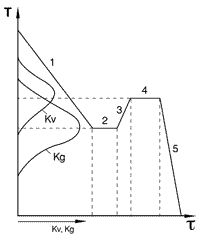 |
Рис. 61. Схема режима термообработки
стекла для получения ситаллов. |
Главной в технологии ситаллов является двухстадийная
термообработка
(рис. 61). Первая стадия - образования
центров кристаллизации - осуществляется для большинства составов шихт
выдержкой при температуре, оптимальной для этого процесса. Для фотоситаллов
изделия после отжига облучают ультрафиолетовыми, рентгеновскими или
- лучами. Проявление скрытого изображения происходит при нагревании стекол
в интервале между температурой размягчения и отжига в течение 8 - 60 мин.
Далее термообработка продолжается при более высоких температурах для завершения
процесса кристаллизации и получения ситалла. На второй стадии изделия
отжигают при температуре, наиболее благоприятной для роста кристаллов.
Жаропрочность, электропроводность, механическая
прочность зависят не только от свойств фаз, но в большей степени от структуры
и потому не являются аддитивными. Плотная микростуктура обеспечивает высокую
твердость и сопротивление абразивному износу. Повышение степени закристаллизованности
увеличивает модуль упругости. Улучшению механических
, термических, электроизоляционных свойств материала и химической стойкости
способствует низкое содержание стекловидной фазы.
Хотя контроль за фазовым составом и структурой в связи с тонкозернистостью
ситаллов осуществляется в основном методами рентгенофазового анализа и
электронной микроскопии, при активном участии петрологов проводится исследование
кинетики зародышеобразования и роста кристаллов, являющихся теоретической
основой главных стадий производства ситаллов.
Вопросы переохлаждения расплавов не чужды петрологии.
Рассмотренные закономерности служат основой объяснения образования природных
стекол и ряда мелкозернистых структур при магматических процессах (глава
II-1), в частности оторочек малоглубинных интрузивных тел. Существенны
они и для методики закалки при проведении эксперимента (см. раздел
IV-4-6).
Дополнительная литература.
Павлушкин Н.М. Основы технологии ситаллов.- М., Стройиздат,
1979.
Бережной А.И. Ситаллы и фотоситаллы.
- М., Машиностроение, 1981.
|